Unlike conventional aircraft with distinct cylindrical fuselage and wing components, the BWB design creates a seamless transition between the body and wings, resembling a flattened, triangular shape. Discover the Best of Blended Wing Body Design Analysis involves evaluating an innovative aircraft configuration that merges the fuselage and wings into a single, smoothly blended structure.
This design offers several potential advantages, including improved aerodynamic efficiency, reduced drag, and increased fuel economy compared to traditional tube-and-wing configurations.
A blended wing body (BWB), alternatively referred to as a blended body, hybrid wing body (HWB), or a lifting aerofoil fuselage, is a type of fixed-wing aircraft characterized by the absence of a clear dividing line between the wings and the main body of the craft.
This design differs from a flying wing, which lacks a distinct fuselage, and a lifting body, which lacks distinct wings. Notably, a BWB design also eliminates the need for a distinct vertical tail.

In a BWB design analysis, engineers assess various factors such as aerodynamic performance, structural integrity, stability, and control characteristics using advanced computational tools, wind tunnel testing, and computer simulations.
They investigate how different parameters, such as wing sweep, aspect ratio, and engine placement, affect the aircraft’s overall performance and handling qualities.
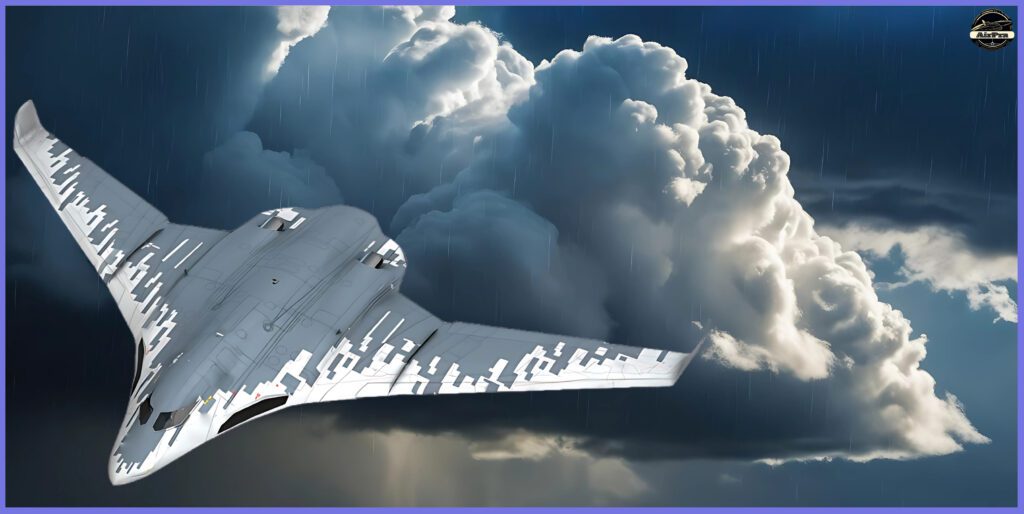
Furthermore, BWB designs offer the potential for greater internal volume, allowing for increased passenger or cargo capacity, as well as novel cabin layout possibilities. However, challenges remain in terms of passenger comfort, emergency egress, and airport infrastructure compatibility.
Overall, the BWB design analysis represents a promising avenue for future aircraft development, with the potential to revolutionize air transportation by offering improved efficiency, capacity, and performance compared to traditional aircraft configurations.

The Evolution of Blended Wing Body (BWB) Aircraft: A Historical Perspective
The evolution of Blended Wing Body (BWB) aircraft represents a significant departure from traditional aircraft design, tracing its roots back to early experiments and conceptualizations.
Initially proposed as a radical departure from conventional tube-and-wing configurations, the BWB concept gained traction in the mid-20th century as advancements in aerodynamics and materials technology enabled engineers to explore more unconventional designs.
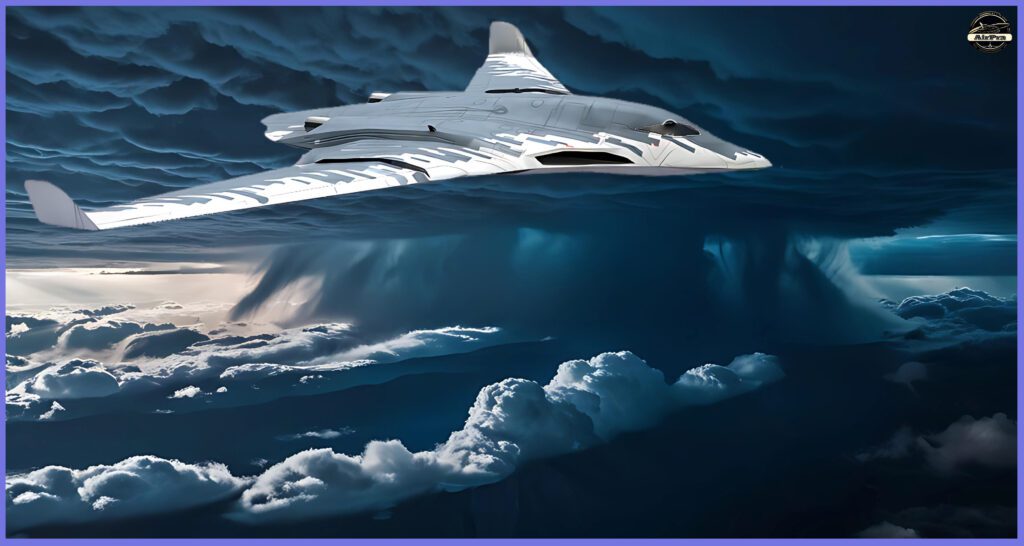
During the early 1920s, Nicolas Woyevodsky formulated a theory for the Blended Wing Body (BWB). Subsequently, the British Westland Dreadnought was constructed after wind tunnel testing.
Regrettably, the aircraft encountered a stall during its maiden flight in 1924, resulting in severe injuries to the pilot and prompting the cancellation of the project.
The concept resurfaced in the early 1940s for the Miles M.26 airliner initiative, leading to the creation of the Miles M.30 “X Minor” research prototype for further exploration. Conversely, the American McDonnell XP-67 prototype interceptor also took flight in 1944 but failed to meet anticipated standards.

In the 1990s, NASA and various aerospace companies, such as McDonnell Douglas and Boeing, began conducting extensive research and development into BWB designs. The potential for enhanced aerodynamic efficiency drove this initiative, reduced fuel consumption, and increased payload capacity.
These efforts resulted in the development of scaled-down prototypes and concept demonstrators, such as the Boeing X-48 and NASA’s X-48B.
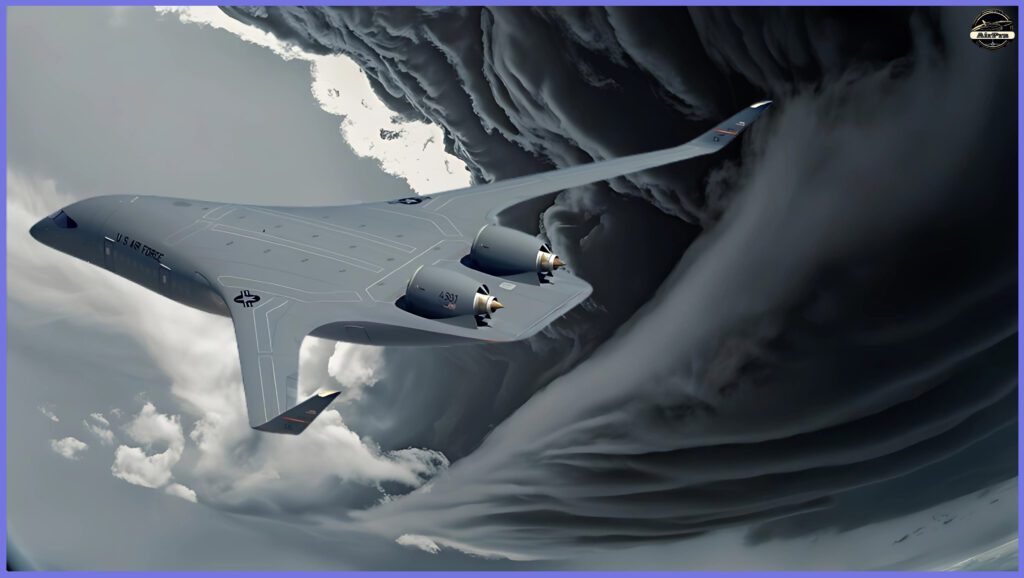
Airbus is investigating the use of a Blended Wing Body (BWB) design as an innovative alternative to conventional aircraft configurations. In mid-2019, the company achieved a milestone with the first flight of a scaled model under the MAVERIC program, aimed at validating new design concepts.
Through this initiative, Airbus seeks to cut CO2 emissions by up to 50% compared to levels recorded in 2005. Additionally, in 2020, as part of its ZEROe project, Airbus unveiled a BWB concept and presented a small prototype to demonstrate the potential of this cutting-edge design.
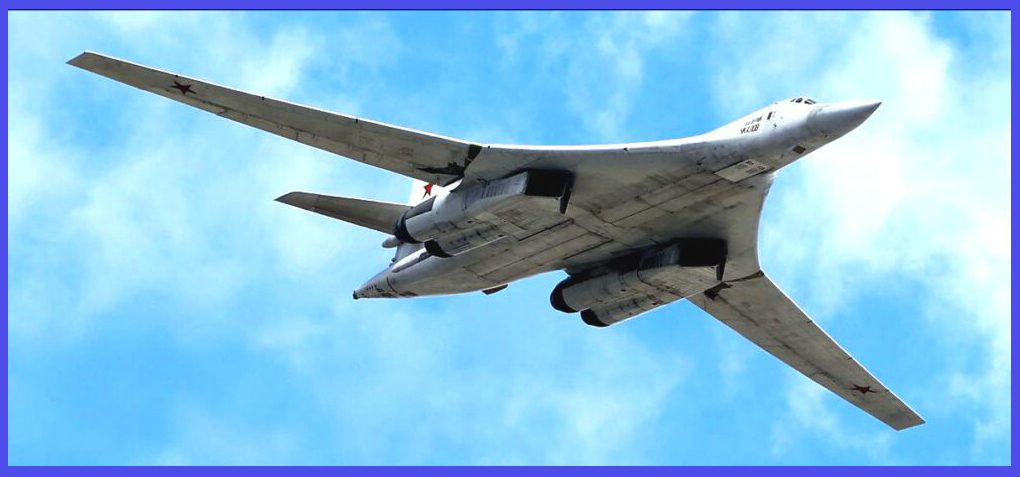
In 2023, California-based startup JetZero unveiled its project, aimed at accommodating passengers and freight and serving as a refueling tanker for military aircraft. Their focus was on the New Midmarket Airplane category, utilizing existing 160kN engines.
Subsequently, in August 2023, the U.S. Air Force awarded a $235-million contract to JetZero, leading to the anticipated first flight of the full-scale demonstrator by the first quarter of 2027.
The primary objective of this contract is to showcase the capabilities of Blended Wing Body (BWB) technology, offering the Department of Defense and the commercial industry additional options for their future air platforms.
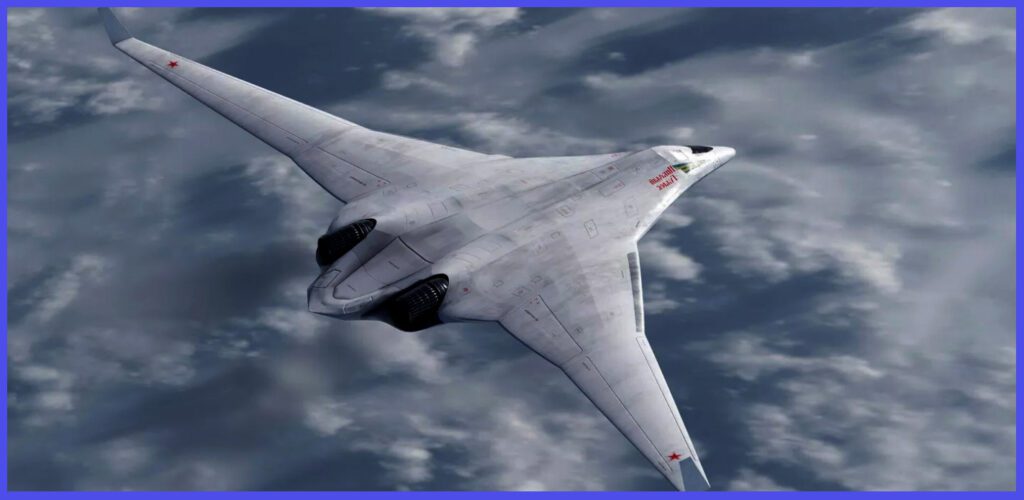
Throughout the early 21st century, continued advancements in computational fluid dynamics (CFD), composite materials, and manufacturing techniques further propelled the development of BWB aircraft. Engineers refined the design to optimize aerodynamic performance, structural integrity, and operational characteristics.
Today, the BWB concept continues to evolve, with ongoing research initiatives focusing on addressing challenges related to passenger comfort, safety, and regulatory certification.
While full-scale commercial implementation of BWB aircraft remains on the horizon, recent advancements suggest that this innovative design paradigm could play a significant role in shaping the future of air transportation, offering potential benefits in terms of environmental sustainability, operational efficiency, and passenger experience.
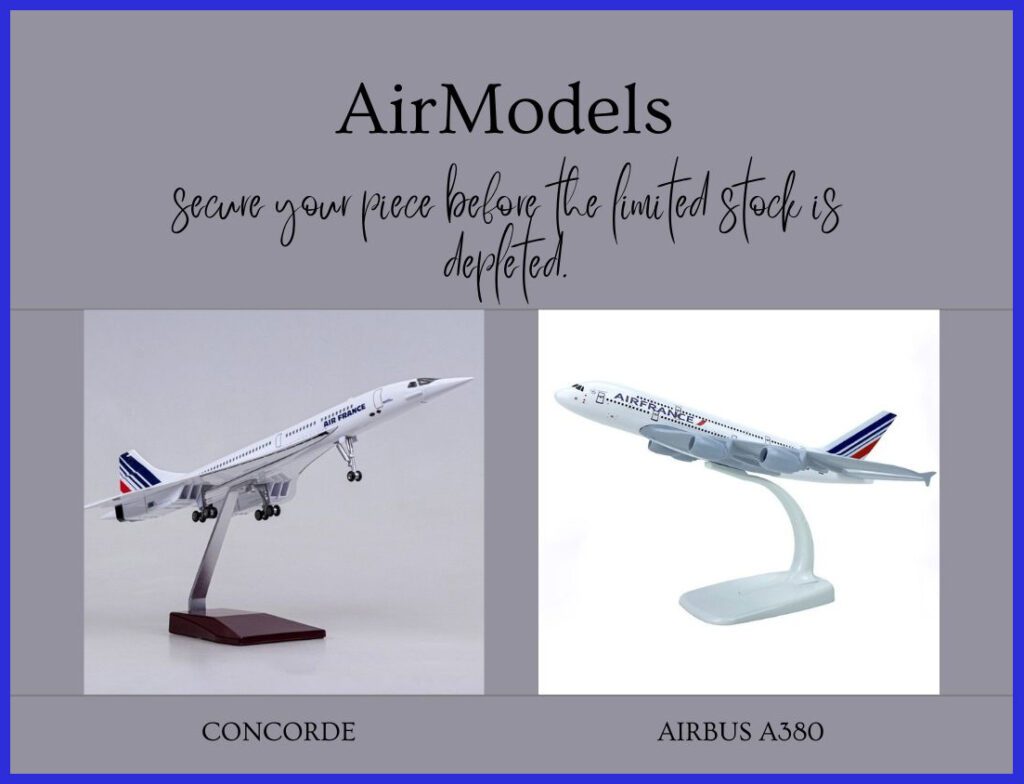
The Design Analysis of Blended Wing Body (BWB) Aircraft
It involves a comprehensive evaluation of various engineering aspects to assess the feasibility, performance, and practicality of this innovative aircraft configuration.
Aerodynamic Analysis: Engineers employ computational fluid dynamics (CFD) simulations and wind tunnel testing to examine airflow around the blended wing body structure. This analysis aids in optimizing the aircraft’s shape, wing sweep, and control surfaces to attain efficient lift generation, minimized drag, and stable flight characteristics.

The expansive interior spaces resulting from the blending present unique structural challenges. NASA has been investigating foam-clad stitched-fabric carbon fibre composite skinning as a method to create uninterrupted cabin space.
Propulsion Integration: The integration of engines into the BWB airframe demands meticulous attention to aerodynamic integration, engine placement, and thrust management. Engineers assess the effects of engine positioning on airflow, performance, noise, and fuel efficiency.
NASA is also exploring the integration of Ultra High Bypass (UHB) ratio jet engines with the hybrid wing body.

Weight and Balance Analysis: Extensive weight estimation and balance calculations are conducted to ascertain the optimal distribution of payload, fuel, and structural components within the BWB design. This analysis aims to achieve a favourable centre of gravity (CG) positioning for safe and stable flight operations.
In a conventional tubular fuselage, approximately 12–13% of the total lift is carried, whereas, in a BWB, this increases to 31–43%, with an intermediate lifting-fuselage configuration carrying 25–32% for a 6.1–8.2% improvement in fuel efficiency, making it better suited for narrowbody-sized airliners.
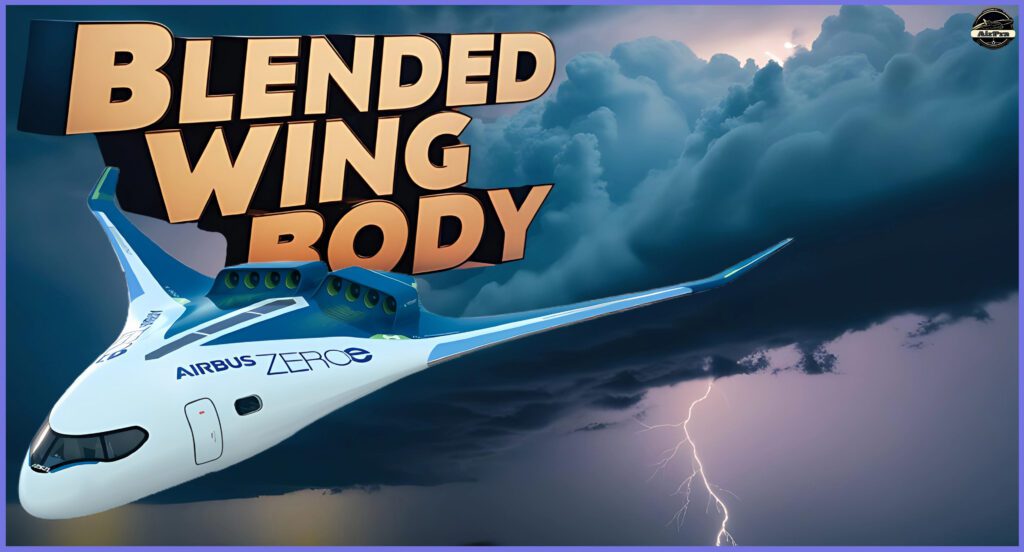
Structural Analysis: Structural engineers meticulously assess the integrity of the BWB design under various flight conditions and loads. They utilize finite element analysis (FEA) to evaluate the strength, stiffness, and fatigue life of the aircraft’s composite or metallic structure, ensuring its capability to withstand aerodynamic forces and structural stresses.
The BWB configuration minimizes the total wetted area, which is the surface area of the aircraft skin, thereby reducing skin drag to a minimum. Additionally, it leads to a thickening of the wing root area, facilitating a more efficient structure and reduced weight compared to a conventional aircraft.

In conclusion, the design analysis of Blended Wing Body (BWB) aircraft represents a pivotal exploration into the future of aviation. Through meticulous examination of aerodynamics, structures, propulsion, operations, and regulatory compliance, engineers aim to unlock the full potential of this innovative aircraft configuration.
By blending fuselage and wing into a seamless, efficient structure, BWB aircraft offer the promise of enhanced aerodynamic performance, increased fuel efficiency, and greater payload capacity.
However, achieving these benefits requires addressing numerous technical challenges, including structural integrity, weight distribution, propulsion integration, and operational considerations.

Despite the complexities involved, ongoing research and development efforts continue to push the boundaries of BWB design, with advancements in computational modelling, materials science, and flight testing driving progress forward.
The first private sector company of American origin, JetZero, is nearing the final stages of revolutionizing BWB design to introduce a new aircraft into service with the US Air Force by 2030.
This initiative is supported by the US Air Force, NASA, and the FAA, aiming to bring the concept to fruition in the real world. The BWB design created by JetZero represents a highly accurate and advanced iteration compared to previous test models developed by others.
With fingers crossed, there is hope that JetZero will overcome all challenges and demonstrate the feasibility of this innovative concept to the world.
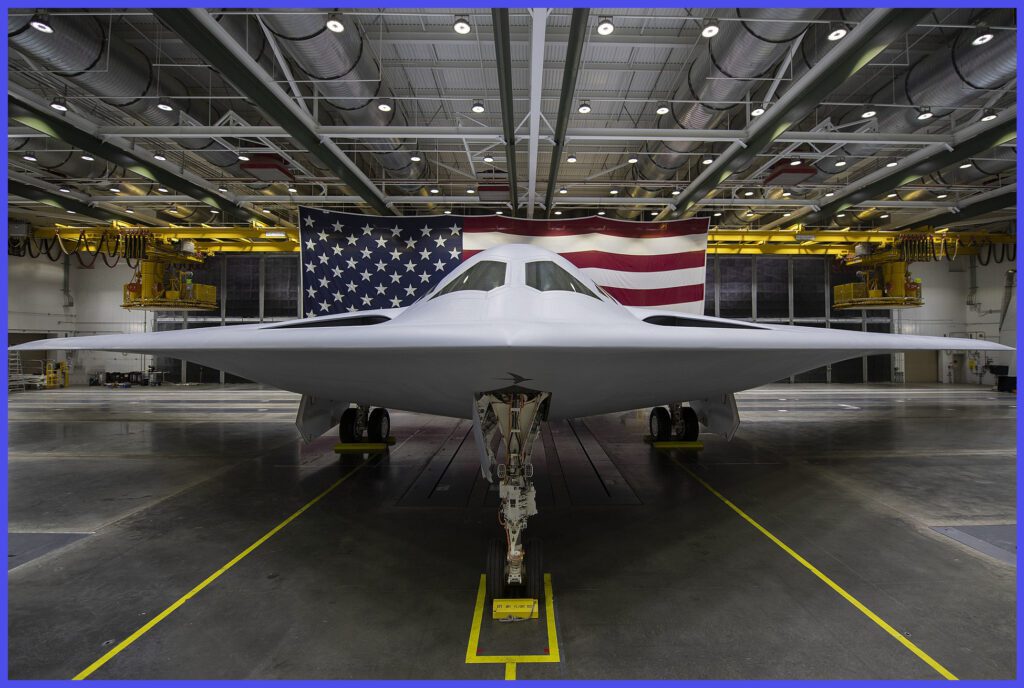
Important Announcement for Our Valued Readers!
After an article is published, it is possible that updates or changes may have occurred beyond the time of publication. Therefore, it is important to be aware that certain information in the article might be outdated. To ensure the most accurate analysis, it is highly recommended to verify the content with the latest sources available.
However, we are dedicated to delivering outstanding articles on military products and global updates. Maintaining quality and smooth operation requires resources. Your support sustains our efforts in providing insightful content.
By purchasing high-quality products through our affiliated links, you help us keep our platform alive and acquire top-notch items. Your unwavering support is invaluable and inspires us to strive further.
We welcome your suggestions and requests for more information, as we value feedback from our readers. If there’s specific defence material or equipment not covered on our site, please share your request in the comments. We’ll strive to research and provide the required information. We sincerely thank you for your unwavering interest in our website, and we eagerly anticipate hearing from you! Enjoy your reading experience!
1 thought on “Discover the Best of Blended Wing Body Design Analysis”