Almost all contemporary military fighter jets use the afterburner combustion component to increase their maximum speed. Let’s delve into How Afterburner Combustion Transforms Jet Performance, whether used for takeoff in short runways with maximum payloads or to defeat adversaries in air-to-air combat.

An afterburner, also known as a reheat system, is a component found in some jet engines, particularly those used in military aircraft and high-performance commercial jets like the earlier Concorde. It is a secondary combustion chamber located downstream of the engine’s primary combustion chamber.
When engaged, the afterburner injects additional fuel into the engine’s exhaust stream, where it ignites and undergoes a secondary combustion process. This produces a significant increase in thrust, enhancing the engine’s power output to achieve maximum speed very quickly.
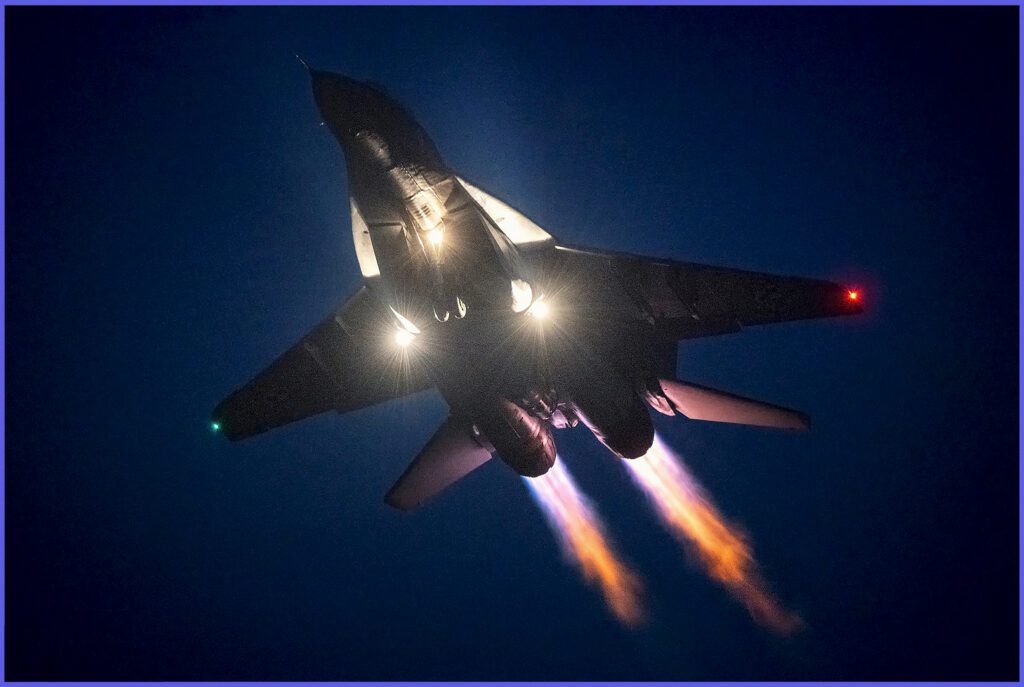
The afterburner works by igniting the fuel-rich exhaust gases that exit the primary combustion chamber, creating a fiery jet exhaust. This expansion of hot gases greatly boosts propulsion force, allowing the aircraft to reach higher speeds or climb more quickly.
However, the afterburner’s operation significantly increases fuel consumption, restricting its usage duration. This means that while the process provides a substantial thrust increase without the added weight of a larger engine, it comes at the cost of reduced fuel efficiency, limiting its use to short periods.

Afterburners are meticulously designed to balance the trade-off between enhanced thrust and increased fuel consumption.
Engineers often describe the afterburning process succinctly: “Jet engines operate ‘wet’ when afterburning and ‘dry’ when not. An engine delivering maximum thrust in ‘wet’ mode is at maximum power, whereas an engine delivering maximum thrust in ‘dry’ mode is at military power.”
Pilots must manage afterburner usage in a calculated manner, typically reserving it for situations requiring maximum power, such as takeoff, combat manoeuvres to dodge incoming missiles, chasing aircraft to reach their level, or during supersonic flight speed tests.
Overall, afterburners play a critical role in enhancing the performance capabilities of jet engines, providing the extra thrust needed for exceptional speed and manoeuvrability in demanding situations.

Flame Acceleration: The Dynamics of Jet Engine Afterburner Design
The dynamics of jet engine afterburner design focus on maximizing thrust and efficiency while managing the challenges of increased fuel consumption and thermal stress. An afterburner is a secondary combustion chamber located behind the turbine section of a jet engine.
When activated, it injects additional fuel into the exhaust stream, which mixes with the remaining oxygen and ignites, creating a powerful expansion of hot gases that dramatically increases thrust.

Crafting an efficient afterburner necessitates careful attention to various critical factors. Engineers focus on achieving efficient fuel blending and ignition, alongside ensuring optimal flame stability to uphold uniform combustion.
Within the afterburner’s internal framework, components such as flame holders or stabilizers are integrated to induce turbulence, facilitating the thorough mixing of fuel and air while sustaining the flame.
Consequently, the exhaust may exhibit shock diamonds, which emerge from shock waves generated by minor differentials in ambient and exhaust pressures.

Apart from the elevation in afterburner exit stagnation temperature, there is a concurrent rise in nozzle mass flow, represented by the sum of afterburner entry mass flow and effective afterburner fuel flow.
However, there’s a decrease in afterburner exit stagnation pressure due to fundamental loss induced by heating, along with friction and turbulence losses. To accommodate the resulting surge in afterburner exit volume flow, adjustments are made by enlarging the throat area of the exit nozzle.
Failure to release pressure could lead to gas flow upstream, potentially triggering a compressor stall.
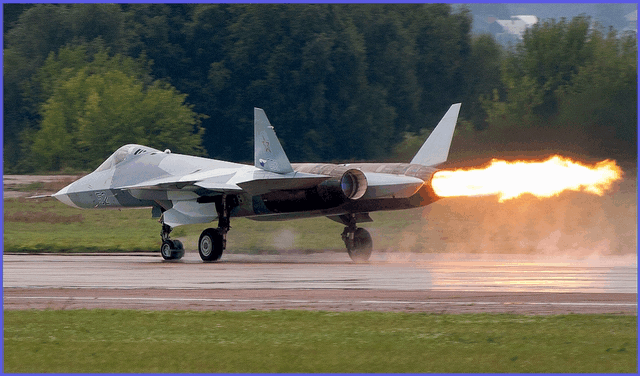
Thermal management is another critical aspect, as the high temperatures generated can strain engine materials. Advanced materials and cooling techniques are used to protect the engine components from heat damage.
Additionally, the design must account for aerodynamic efficiency to minimize drag and optimize the thrust-to-fuel consumption ratio. Overall, the dynamics of afterburner design are about balancing enhanced performance with efficiency and durability.

Issues Associated with Afterburners
The main issues with afterburners include their high fuel consumption, which significantly reduces the aircraft’s range and operational duration. They generate extreme thermal stress, potentially leading to increased wear and maintenance requirements. Afterburners also produce a high infrared signature, making aircraft more detectable to heat-seeking missiles.
Additionally, their use results in increased maintenance costs due to the added complexity and strain on engine components. Hence, afterburners are only used for short-duration, high-thrust requirements. These include heavy-weight or short-runway take-offs, assisting catapult launches from aircraft carriers, and during air combat.

In conclusion, afterburners in contemporary military jets offer vital speed enhancements, crucial for rapid response and combat effectiveness.
Additionally, they facilitate short takeoffs, aiding in operations from confined spaces like aircraft carriers. However, challenges such as high fuel consumption and maintenance costs necessitate careful management to fully exploit their advantages.