Its combat-proven track record and ability to operate from aircraft carriers further enhance its strategic significance, solidifying its position as a vital defence asset for naval and allied forces worldwide, both in 2023 and beyond. Equipped with state-of-the-art avionics and radar systems, the F/A-18 Hornet can engage in air-to-air combat and ground-attack missions with unparalleled precision, ensuring its effectiveness in modern warfare.
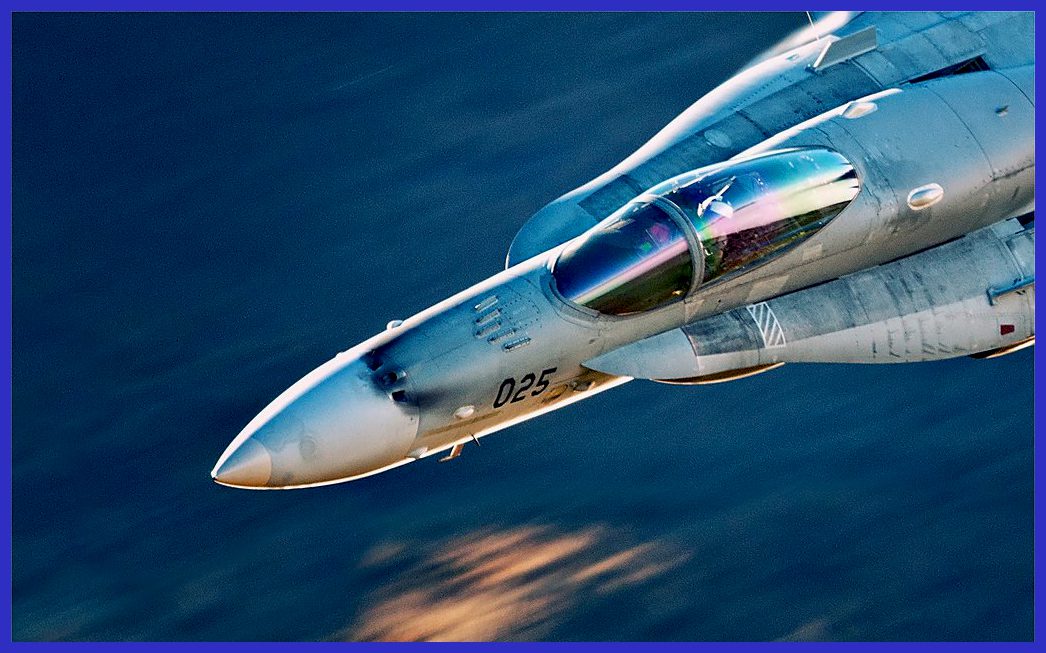
The Genesis of Northrop / McDonnell Douglas F/A-18 Hornet
The origins of the F-18 can be traced back to the 1970s when the U.S. Navy found itself in need of a new aircraft program. The primary objective was to procure a multirole aircraft that would replace the Douglas A-4 Skyhawk, the A-7 Corsair II, and the ageing fleet of McDonnell Douglas F-4 Phantom IIs. Furthermore, the Navy aimed to complement its existing F-14 Tomcat and sought a highly agile and rugged fighter capable of operating from aircraft carriers and performing both air-to-air and ground-attack missions.
In August 1973, Congress stepped in and mandated that the Navy pursue a more cost-effective alternative to the F-14. During the same year, Secretary of Defense James R. Schlesinger instructed the Navy to evaluate competitors in the Air Force’s Lightweight Fighter (LWF) program, which included the General Dynamics YF-16 and Northrop YF-17. By that time, the YF-16 had already been chosen by the USAF, as F-16.
In 1975, the Navy officially announced its selection of the YF-17 design to meet its future requirements. However, considering the unique needs of the Navy, they requested McDonnell Douglas and Northrop to collaborate and redesign the YF-17, developing a new aircraft based on its principles.
Finally, on 1 March 1977, Secretary of the Navy W. Graham Claytor made the momentous announcement that the F-18 would be the series, named “Hornet.” With this decision, the F-18 Hornet entered into service, becoming a vital asset for the U.S. Navy’s carrier-based operations.
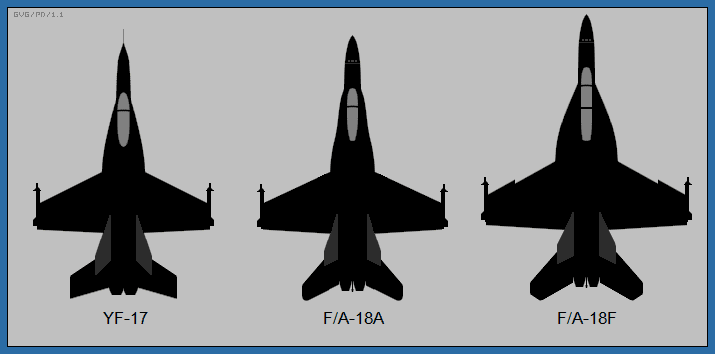
The Development of Northrop / McDonnell Douglas F/A-18 Hornet
In the context of the F-18 project, the two collaborating companies agreed to divide component manufacturing equally, with McDonnell Douglas being responsible for the final assembly. The specific tasks assigned to each company were defined, as McDonnell Douglas would undertake the construction of the wings, stabilators, and forward fuselage, while Northrop would focus on the centre and aft fuselage and vertical stabilizers. It’s worth noting that McDonnell Douglas served as the prime contractor for the naval versions, while Northrop assumed the prime contractor role for the F-18L land-based version, with the intention of selling it in the international market.
To enable carrier operations, a series of specific modifications were made. The airframe, undercarriage, and tailhook were reinforced for carrier suitability. Folding wings and catapult attachments were integrated, and the landing gear was widened to meet carrier-specific requirements. Additionally, McDonnell responded to the Navy’s demands by increasing fuel capacity by 4,460 pounds (2,020 kg), achieved through enlarging the dorsal spine and adding a 96-gallon fuel tank to each wing. Enlargements were also made to the wings, stabilators, and aft fuselage by 4 inches (102 mm). Optimizing performance further, the engines were canted outward at the front, resulting in a 10,000 lb (4,540 kg) increase in overall gross weight, bringing it close to 37,000 lb (16,800 kg).
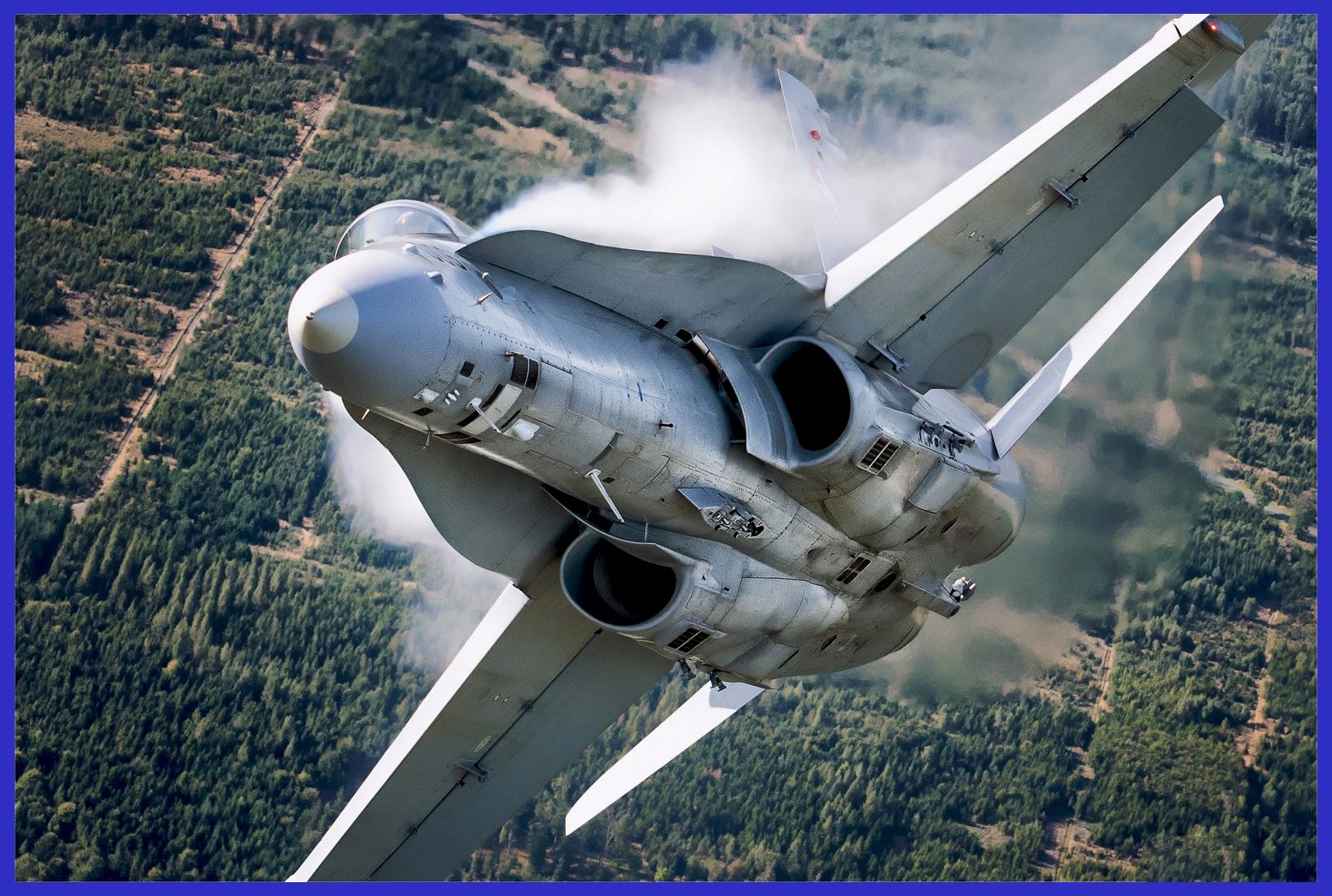
Finally, a significant update was made to the YF-17’s control system, which was replaced with a fully digital fly-by-wire system featuring quadruple redundancy. This particular enhancement was noteworthy, as it marked the first implementation of such a system in a production fighter aircraft.
Originally, the initial plans involved the acquisition of a total of 780 aircraft with three distinct variants: the single-seat F-18A fighter, the A-18A attack (A) aircraft, which differed solely in avionics, and the dual-seat TF-18A, retaining the full mission capability of the F-18 but with a reduced fuel load. However, over the subsequent two years, significant enhancements in avionics and multifunction displays were implemented, along with a redesign of external store stations, leading to the combination of A-18A and F-18A into a single aircraft.
Consequently, starting in 1980, the aircraft began being referred to as the F/A-18A and the official designation was announced on 1 April 1984. The trainer TF-18A was subsequently renamed F/A-18B. On 12 April 1980, the first production F/A-18A took flight, and it was eventually deployed for service by the U.S. Navy and Marine Corps. After the production of 380 F/A-18As, the manufacturing focus shifted to the F/A-18C in September 1987.
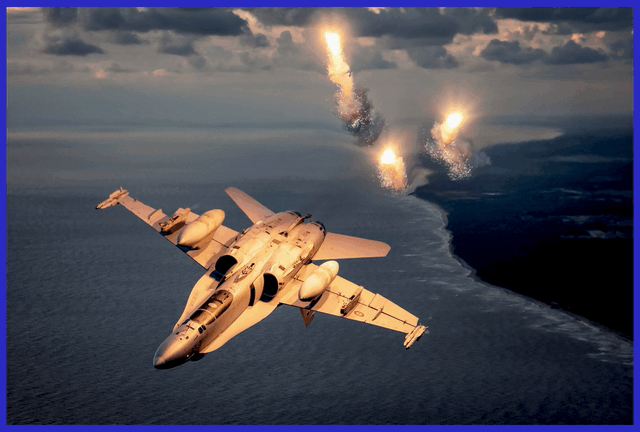
Throughout the years, the F/A-18 Hornet has earned a reputation as a highly successful and reliable multirole fighter, becoming an integral part of the military inventories in numerous countries worldwide. Its continuous evolution led to the development of more advanced variants like the F/A-18E/F Super Hornet, ensuring its enduring service well into the 21st century.
Over the years, the F/A-18 Hornet family has evolved and expanded to include various variants, each with specific capabilities tailored to meet the requirements of different branches of the military, both for domestic and foreign clients. As of now, Four major variants have been developed since its inception, which include the F/A-18A/B, F/A-18C/D, and the more advanced F/A-18E/F Super Hornet. However, based on its advanced avionics, radar systems, and long-range capacity, the Boeing engineers have developed an electronic warfare specialist platform, which can be seen in the EA-18G Growler variant, making it an integral asset for the U.S. Navy & Marine Corps, and various allied nations in modern aerial warfare. Below, we are discussing this latest variant in detail.
The Genesis of Boeing F/A-18E/F Super Hornet
The genesis of the Boeing F/A-18E/F Super Hornet can be traced back to the early 1990s when the U.S. Navy sought to address the limitations of the F-18 A & B models and the rapid ageing of its existing fleet of F-14 Tomcats. The primary goal was to develop a more capable and advanced carrier-based strike fighter to replace both. Boeing, which had acquired McDonnell Douglas (the original developer of the F/A-18 Hornet), took the initiative to modernize the design and develop an upgraded version. The result was the F/A-18E/F Super Hornet (E-single seater and F-tandem seater), an evolution of the original F/A-18 Hornet family with numerous improvements and enhancements.
The F/A-18E/F Super Hornet features a larger airframe, enhanced fuel capacity, and upgraded avionics. The design integrates cutting-edge advancements in radar systems, sensors, and electronic warfare capabilities. Its propulsion is supported by more powerful General Electric F414 engines, which significantly boost thrust and operational range. Thanks to these improvements, the Super Hornet can carry a larger payload and sustain longer missions compared to its predecessor. Additionally, the aircraft can be adapted into an airborne tanker by incorporating an external air-to-air refuelling system.
The inaugural flight of the F/A-18E Super Hornet occurred in November 1995, followed by the F/A-18F two-seat variant in 1996. Full-rate production began in September 1997, subsequent to the merger of McDonnell Douglas and Boeing. The U.S. Navy formally integrated the Super Hornet into service in 1999, and since then, it has become the primary carrier-based strike fighter for the Navy, eventually replacing the older F-14 Tomcats, which were retired in 2006.
The F/A-18E/F Super Hornet’s versatility, advanced capabilities, and capacity to operate from aircraft carriers have established it as a critical asset in contemporary naval aviation. Its triumphs have also generated export orders from numerous allied nations. The Royal Australian Air Force (RAAF), which has utilized the F/A-18A as its primary fighter since 1984, placed an order for the F/A-18F in 2007, further consolidating its position as a dominant multirole fighter aircraft on the international stage.
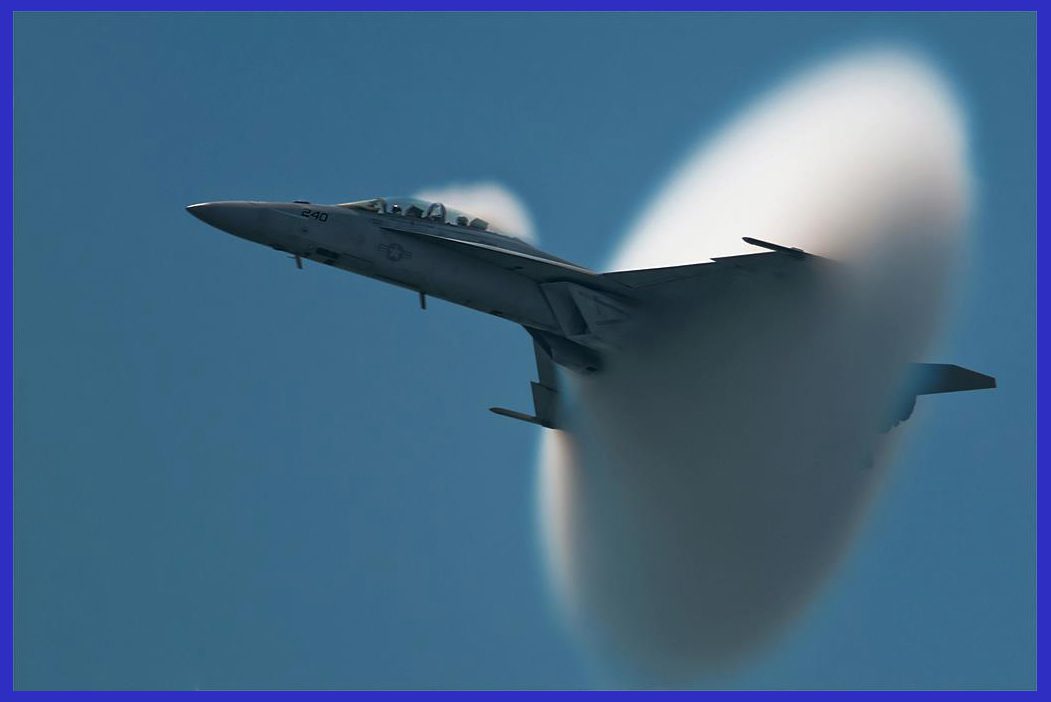
Development story of the Boeing F/A-18E/F Super Hornet
The development story of the Boeing F/A-18E/F Super Hornet is rooted in the need to address the limitations of the original F/A-18 Hornet and fulfil the requirements for a more advanced carrier-based strike fighter for the U.S. Navy’s 21st-century warfare strategy. With this vision in mind, the Super Hornet program was initiated and can be summarized in the following key steps:
Design and Upgrades: To meet the need for a multi-role fighter that could supplement the bigger and more expensive Grumman F-14 Tomcat, which was used for fleet defence interceptor and air superiority tasks, the Navy recommended that the YF-17 be modified into the larger F/A-18 Hornet. Based on the already-existing F/A-18 Hornet airframe, the F/A-18E/F Super Hornet underwent several important improvements and alterations. As a result, the wing area was increased to improve aerodynamics, and the fuselage was stretched to increase internal fuel capacity. Its fighting capabilities were further improved by the addition of sophisticated avionics, radar, and sensor suites.
Enhanced Performance: The Super Hornet is equipped with more powerful General Electric F414 engines, delivering increased thrust and superior performance when compared to the original F/A-18 Hornets. The enhanced engine capabilities enable greater speed, extended range, and improved payload-carrying capabilities. The testing phase extended through 1999, concluding with comprehensive sea trials and aerial refuelling demonstrations. A total of 3,100 test flights were conducted, covering an impressive 4,600 flight hours. The Super Hornet successfully underwent U.S. Navy operational tests and evaluations in 1999 and received approval in February 2000.
Following the retirement of the F-14 in 2006, all of the Navy’s combat jets have been Super Hornet variants until the induction of the F-35C Lightning II, which took its place by excelling in all aspects. The Navy deems the acquisition of the Super Hornet a resounding success, meeting cost-effectiveness, scheduled delivery, and weighing 400 lbs less than the anticipated requirements.
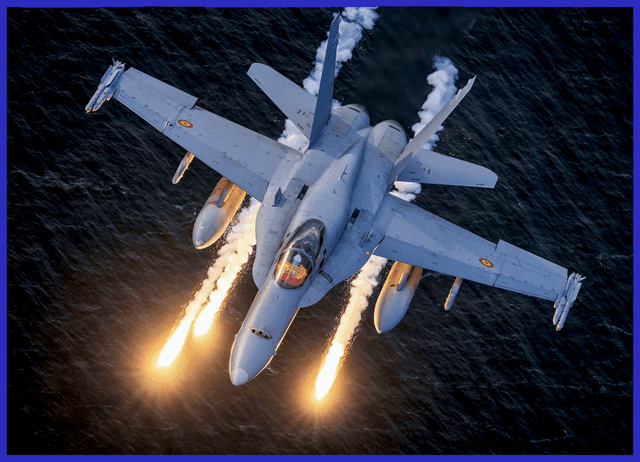
Enhancements and modifications: The Block II Super Hornet represents the next updated version, featuring various enhancements. These improvements include an upgraded active electronically scanned array, APG-79 (AESA) radar, larger displays, the joint helmet-mounted cueing system, and several other avionics replacements. Notably, the avionics and weapons systems initially developed for the prospective production version of the fifth-generation Boeing X-32 JSF were utilized in the upgrades made to the Block II Super Hornet.
In 2008, Boeing engaged in discussions with the U.S. and Australian military regarding the development of a Super Hornet Block III. This updated version boasted additional stealth capabilities and extended range. Subsequently, in 2010, Boeing presented the “International Roadmap” to potential Super Hornet customers. The roadmap included various enhancements, such as conformal fuel tanks, improved engines, an enclosed weapons pod (EWP), a next-generation cockpit, a new missile warning system, and an internal infrared search and track (IRST) system.
The EWP featured four internal stations for munitions, and a single aircraft had the capacity to carry up to three EWPs, with the capability of housing up to 12 AMRAAMs and 2 Sidewinders. Moreover, the next-generation cockpit was equipped with a 19 x 11-inch touch-sensitive display, providing advanced functionality and user interaction.
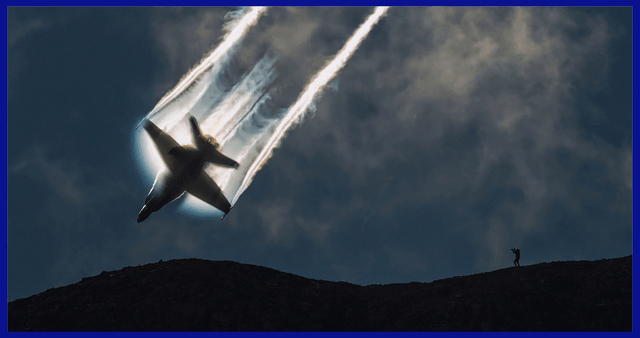
Advanced Super Hornet Block III and planned end of production: Boeing and Northrop Grumman self-funded the development of a prototype for the Advanced Super Hornet. The prototype incorporates several key features, including a 50% reduction in frontal radar cross-section (RCS), conformal fuel tanks (CFT), and an enclosed weapons pod design. Flight tests of the Advanced Super Hornet commenced on 5 August 2013 and spanned three weeks, focusing on evaluating the performance of CFTs, the enclosed weapons pod (EWP), and signature enhancements.
The results of the Advanced Super Hornet’s flight tests were reportedly well-received by the U.S. Navy, which holds hopes that it will offer viable procurement options in the future. Moreover, similar Block-III updates were also integrated into the EA-18G Growler variant, employing CFTs to free up underwing space and reduce drag margin, benefiting the Next Generation Jammer program.
In 2013, the U.S. Navy was considering the widespread adoption of CFTs, which would allow the Super Hornet to carry 3,500 lbs of additional fuel. Moreover, the highly expensive F-35C Lightning II, along with the maintenance cost of the 5th generation fighter in deck-based operations, creates budgetary pressure, which also has positive impacts on the production of the Super Hornet block-III standard. In fact, flight testing demonstrated that CFTs could slightly reduce drag while expanding the combat range by 260 nautical miles (480 km). However, Boeing also stated that the CFTs do not add any cruise drag, but they acknowledged a negative impact on transonic acceleration due to increased wave drag.
Taking these factors into account, General Electric’s enhanced performance engine (EPE) was proposed as a mitigating solution, increasing the F414-GE-400’s power output from 22,000 to 26,400 lbf (98 to 117 kN) of thrust per engine. In 2019, Boeing secured a substantial $4 billion contract to supply 78 Block III Super Hornets to the Navy, with deliveries scheduled until fiscal 2021. The Navy plans to upgrade all Block II aircraft to Block III variants by 2033 through year-to-year agreements.
However, the U.S. Navy halted plans to make CFTs (Conformal Fuel Tanks) standard on all Block III Super Hornets in 2021 due to cost, schedule, and performance concerns. Despite this setback, continuous advancements remain a primary objective. On February 23, 2023, Boeing announced its intentions to terminate Super Hornet production by 2025 due to waning interest in the aircraft and competition from the F-35.
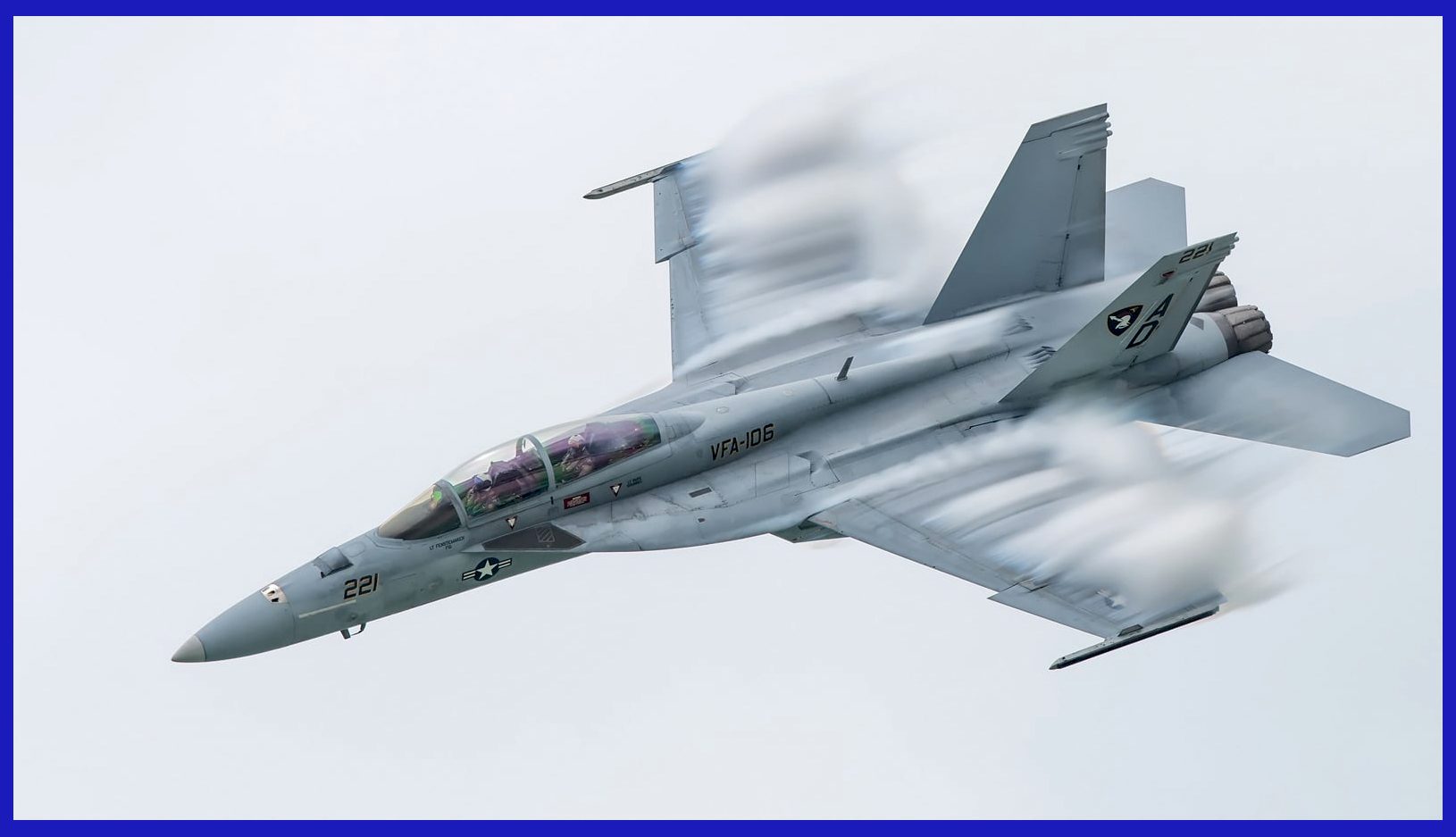
An Analysis of the Present-Day Boeing F/A-18E/F Super Hornet Design
As we delve into an analysis of this exceptional aircraft’s features, we uncover a host of enhancements that have solidified its position as a dominant force in the skies. From its strengthened airframe and advanced avionics to its potent electronic warfare capabilities and network-centric warfare integration, the Super Hornet exemplifies versatility, performance, and agility, setting new standards for combat effectiveness on the modern battlefield.
Airframe and Aerodynamics: The F/A-18E/F Super Hornet maintains the twin-engine, twin-tail design of its predecessor, the F/A-18 Hornet. To accommodate the increased weight and additional fuel capacity, the aircraft’s airframe has been reinforced. Extensive optimization of its aerodynamics has been carried out to enhance agility, speed, and carrier operations. The Super Hornet represents a substantial advancement, being around 20% larger and 7,000 lb (3,200 kg) heavier in empty weight, with a maximum weight increase of 15,000 lb (6,800 kg) compared to the original Hornet from the 1980s.
This upgrade enables the Super Hornet to carry 34% more internal fuel, resulting in a remarkable 44% increase in mission range and a 50% boost in endurance over the previous Hornet design. Considering the significant weight difference from the legacy Hornet, the catapult and arresting systems have been tailored to ensure a life airframe time of 8,000 to 10,000 hours, specifically meeting the Block-III standards.
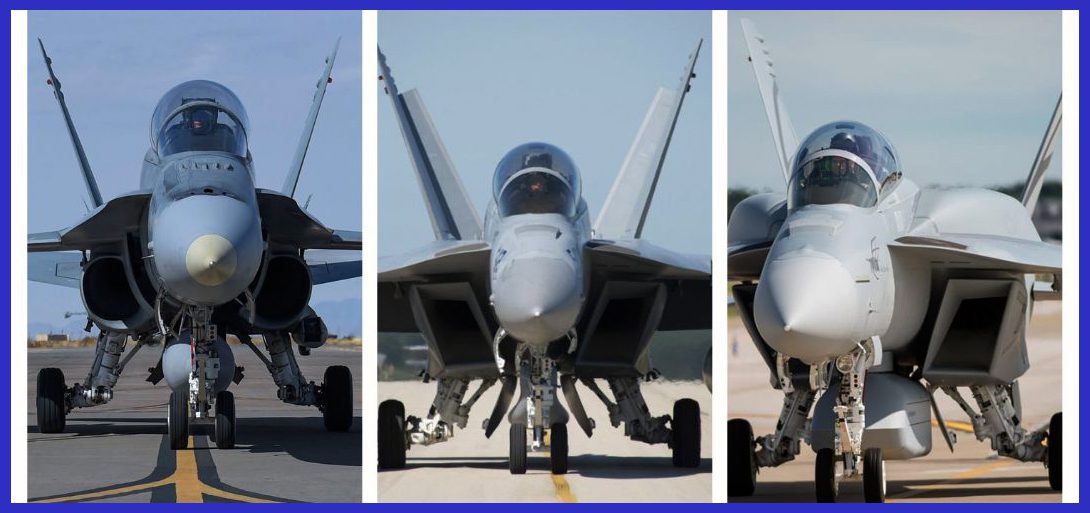
Air Intake Design Differences: The F/A-18 Hornets and F/A-18E/F Super Hornets feature notable variations in air intake design. The older F/A-18 Hornets, including the F/A-18A/B/C/D variants, are equipped with a traditional “D-shaped” air intake design, where a splitter plate separates the two engine intakes. On the other hand, the newer F/A-18E/F Super Hornets exhibit an upgraded “rectangular” air intake design, characterized by larger openings and revised duct geometry, which significantly enhances airflow to the more powerful engines. This improved design results in enhanced engine performance, leading to higher thrust output and greater fuel efficiency.
Super Hornets RCS Measures: The F/A-18E/F’s radar cross-section (RCS) is significantly reduced from certain aspects, particularly the front and rear. The design of the engine inlets contributes to the reduction of the aircraft’s frontal RCS, with the alignment of the leading edges specially designed to scatter radiation sideways. Fixed fanlike reflecting structures in the inlet tunnel enhance stealth by diverting radar energy away from the rotating fan blades.
The Super Hornet also utilizes panel joint serration and edge alignment to effectively direct reflected waves away from the aircraft at narrow angles. Attention to removing or filling unnecessary surface join gaps and resonant cavities further reduces the aircraft’s radar signature. These meticulous efforts and technological advancements play a vital role in enhancing the Super Hornet’s survivability in various operational scenarios.
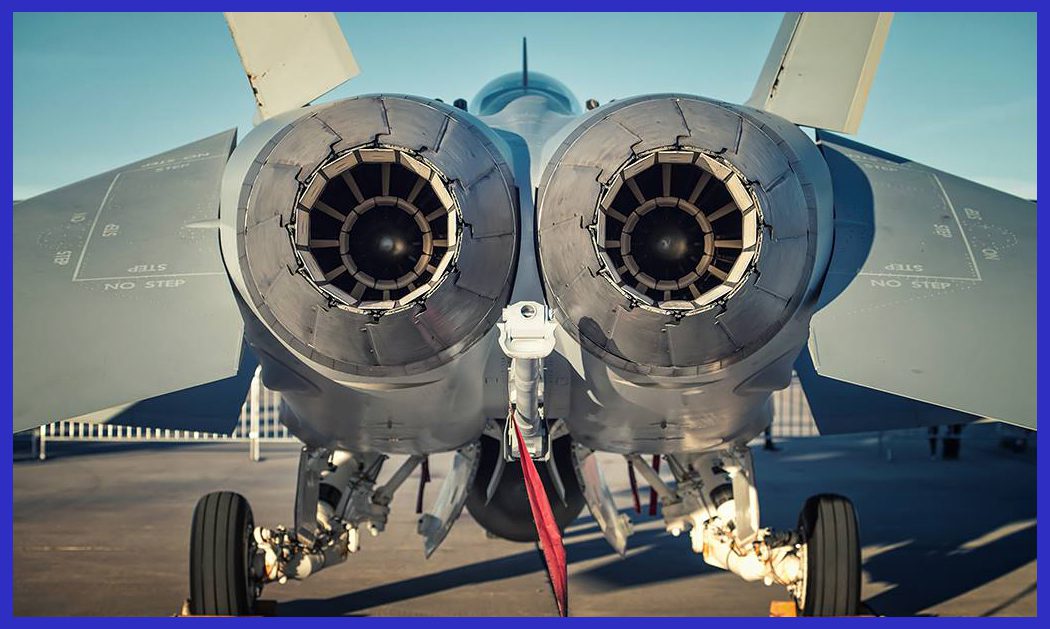
Super Hornet Tactical Airborne Tanker with ARS: The Super Hornet, unlike the previous Hornet, has also been designed to be equipped with an aerial refuelling system (ARS) or “buddy store,” enabling it to perform the critical tactical airborne tanker role that the Navy had lost with the retirement of the A-6 Intruder and Lockheed S-3B Viking tankers. The ARS includes an external 1,200 L tank with a hose reel on the centerline pylon, in addition to four external 1,800 L tanks, along with its internal fuel capacity, allowing the aircraft to carry a total of 29,000 lb (13,000 kg) of fuel for specific tactical missions, enabling operations close to the enemy borderline.
Avionics and Sensors: The Super Hornet is equipped with state-of-the-art avionics, boasting a contemporary glass cockpit that integrates large multifunction displays, digital fly-by-wire flight controls, and a sophisticated mission system. One of its prominent features is the powerful AN/APG-79 AESA radar, renowned for its exceptional detection and tracking capabilities, which substantially enhances situational awareness and provides resistance against electronic jamming. To accommodate additional fuel capacity and accommodate future avionics upgrades, the fuselage has been stretched by 34 inches (86 cm). Furthermore, a remarkable 25% increase in wing area further enhances the aircraft’s performance capabilities.
In May 2007, the first Super Hornet upgraded with the Joint Helmet Mounted Cueing System (JHMCS) was delivered. The JHMCS enhances multi-purpose situational awareness, including high-off-boresight missile cuing. Additionally, the Shared Reconnaissance Pod (SHARP) is a high-resolution, digital tactical aerial reconnaissance system that boasts advanced day/night and all-weather capabilities. Furthermore, the Multifunctional Information Distribution System low-volume communication terminal is currently undergoing an upgrade with the MIDS-JTRS (joint tactical radio) system. This upgrade enables a tenfold increase in bandwidth and ensures compatibility with the Joint Tactical Radio System standards.
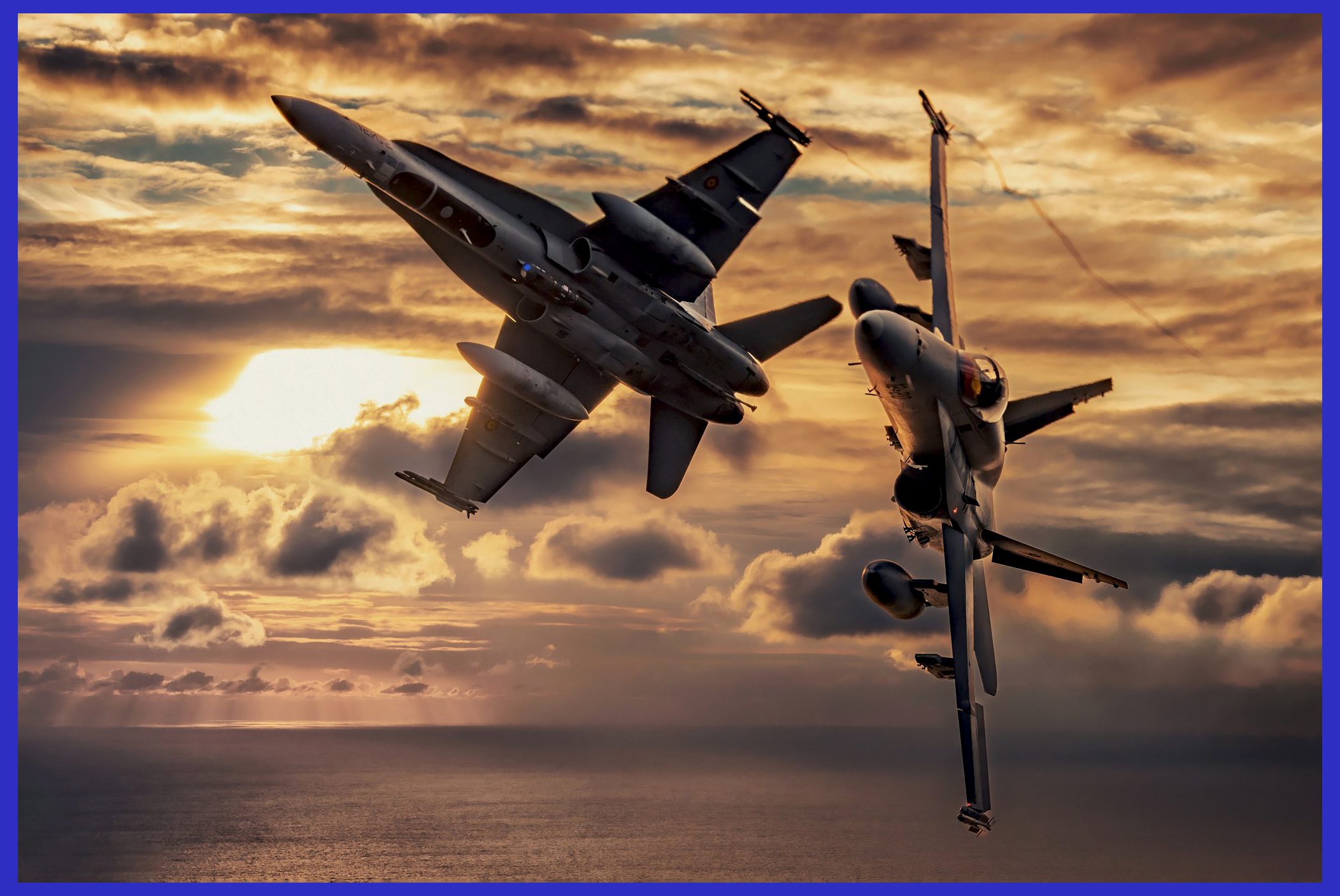
Performance: The Super Hornet is equipped with twin General Electric F414 engines, derived from the F404 engine of its predecessor, the Hornet. These engines deliver an extraordinary 35% increase in thrust across most of the flight envelope, resulting in an outstanding thrust-to-weight ratio and remarkable manoeuvrability. Such capabilities enable the aircraft to execute agile and dynamic flight operations with ease. Notably, the Super Hornet’s impressive performance translates into extended range and endurance, enhancing its versatility in carrying out diverse missions with heightened efficiency and effectiveness.
As of the present day, the F/A-18E/F Super Hornet remains a significant part of the U.S. Navy’s aviation fleet and continues to undergo upgrades and improvements to maintain its relevance and combat effectiveness in the ever-changing landscape of modern aerial warfare. Furthermore, the Super Hornet’s export variants are in service with Australia and Kuwait, further demonstrating its popularity and success on the international stage.
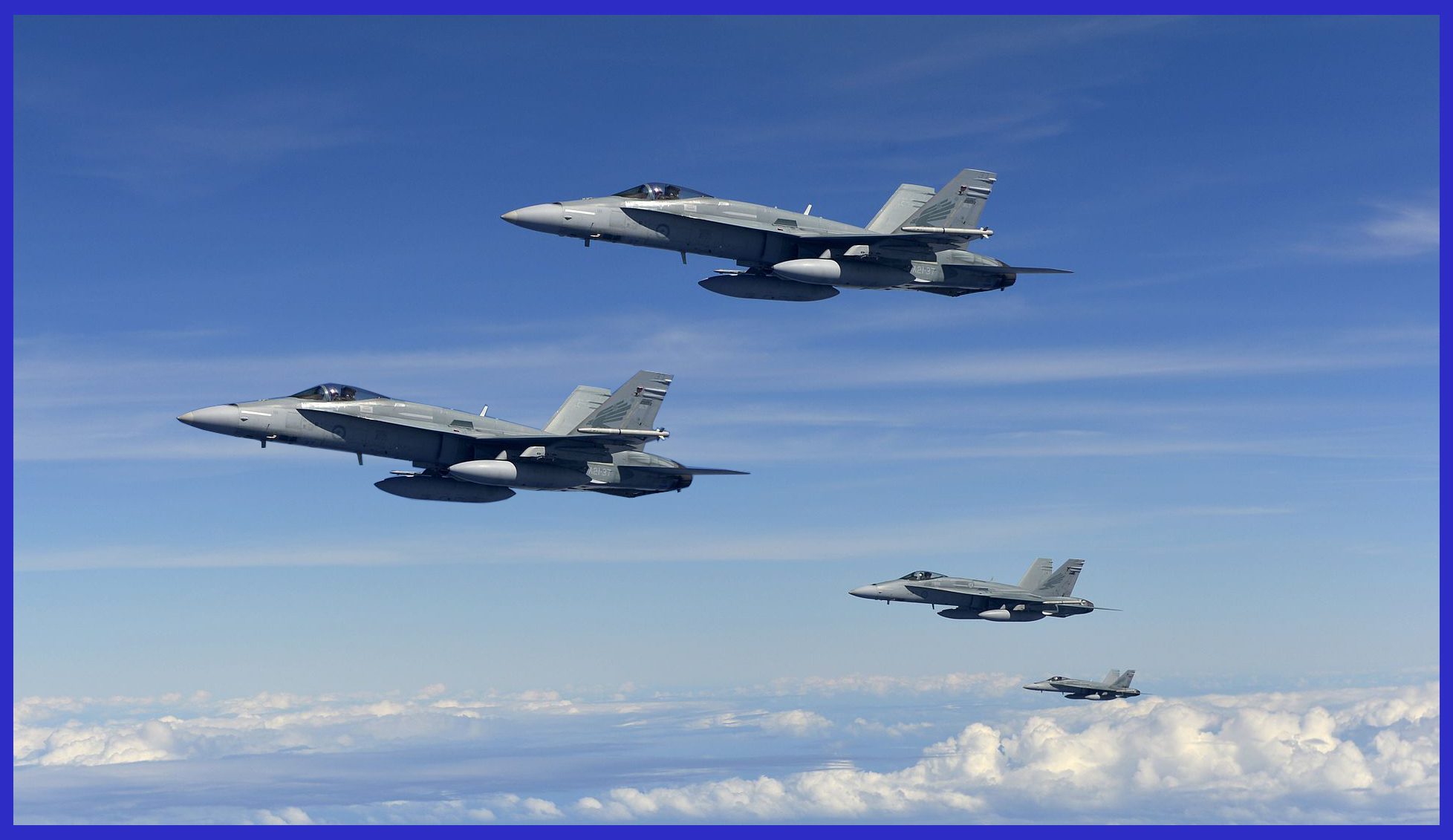
Finally, Let’s Delve into the Genesis of the Boeing EA-18G Growler Variant
The Boeing EA-18G Growler is an advanced electronic warfare aircraft of American origin, built on the F/A-18F Super Hornet airframe. Its primary role is the suppression of enemy air defences, equipped with specialized jamming pods and advanced electronic attack systems that enable it to effectively disrupt and neutralize enemy radars and communication systems. The EA-18G serves as a force multiplier with its cutting-edge avionics, providing crucial support and protection to friendly aircraft during missions.
Its versatility, extended range, and ability to operate from aircraft carriers make it a vital asset for the U.S. Navy and its allied forces, ensuring dominance in the electromagnetic spectrum and enhancing battlefield effectiveness. Production of the EA-18G commenced in 2007, and it was introduced into operational service with the US Navy in late 2009, taking over the role from the Northrop Grumman EA-6B Prowlers, which had served the United States Navy for nearly five decades.
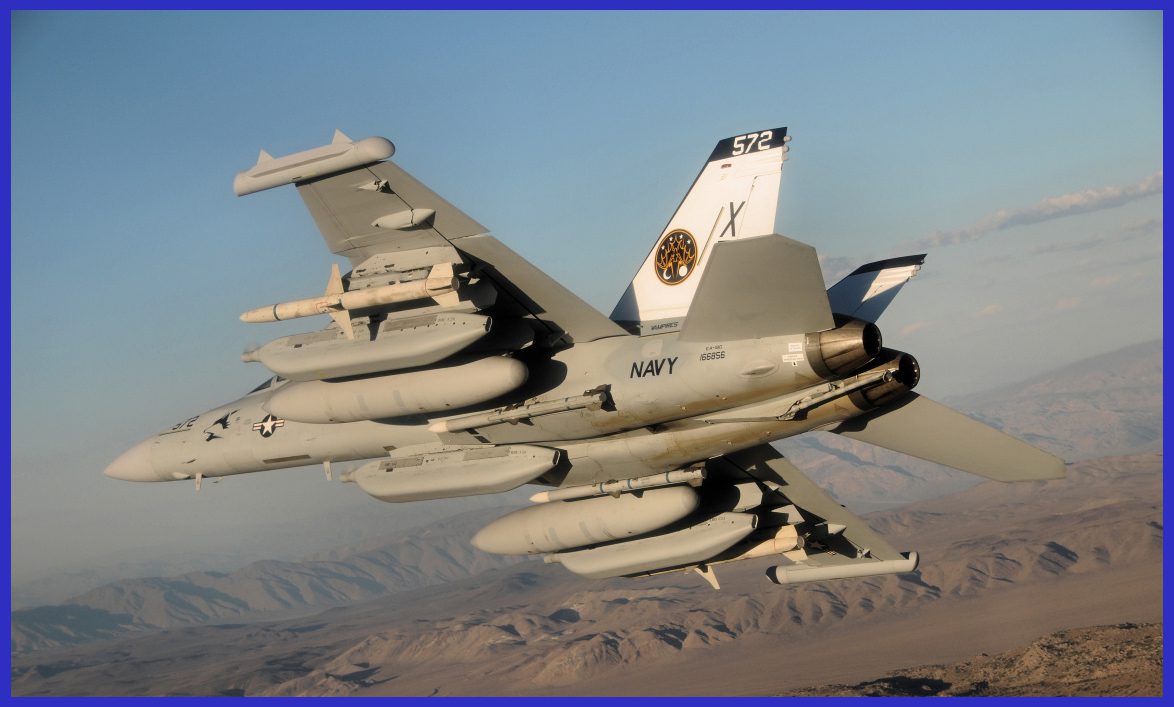
EA-18G Growler Testing and Development
The EA-18G Growler program was initiated to address the requirement of replacing the ageing EA-6B Prowler, the former electronic warfare aircraft. The United States Navy aimed to create an upgraded platform based on the F/A-18F Super Hornet airframe, integrating advanced electronic attack capabilities. Consequently, on 15 November 2001, Boeing achieved a successful initial flight demonstration of the F/A-18F, specifically the “F-1” model equipped with the ALQ-99 electronic warfare system, which served as the basis for the EA-18 Airborne Electronic Attack (AEA) concept aircraft.
Following a series of tests in December 2003, the US Navy awarded the development contract for the EA-18G to Boeing. As the primary contractor, Boeing assumed responsibility for the construction of the forward fuselage and wings, as well as the final assembly. Simultaneously, Northrop Grumman was designated as the principal airframe subcontractor, tasked with supplying the centre and aft fuselage components, along with the principal electronic combat system. Additionally, the power supply included General Electric F414-GE-400 turbofan engines.
Based on the contract and extensive tests, the first EA-18G test aircraft entered production on 22 October 2004. The maiden flight of the first test aircraft, known as EA-1, took place in August of the same year after it was rolled out on 3 August 2006. Two models were created for testing: EA-1, which primarily supported ground testing in the Air Combat Environment Test and Evaluation Facility (ACETEF) anechoic chamber, and EA-2, which was used for developmental testing as the AEA (Airborne Electronic Attack) system. Later on, the number of test aircraft was increased to five by 2008.
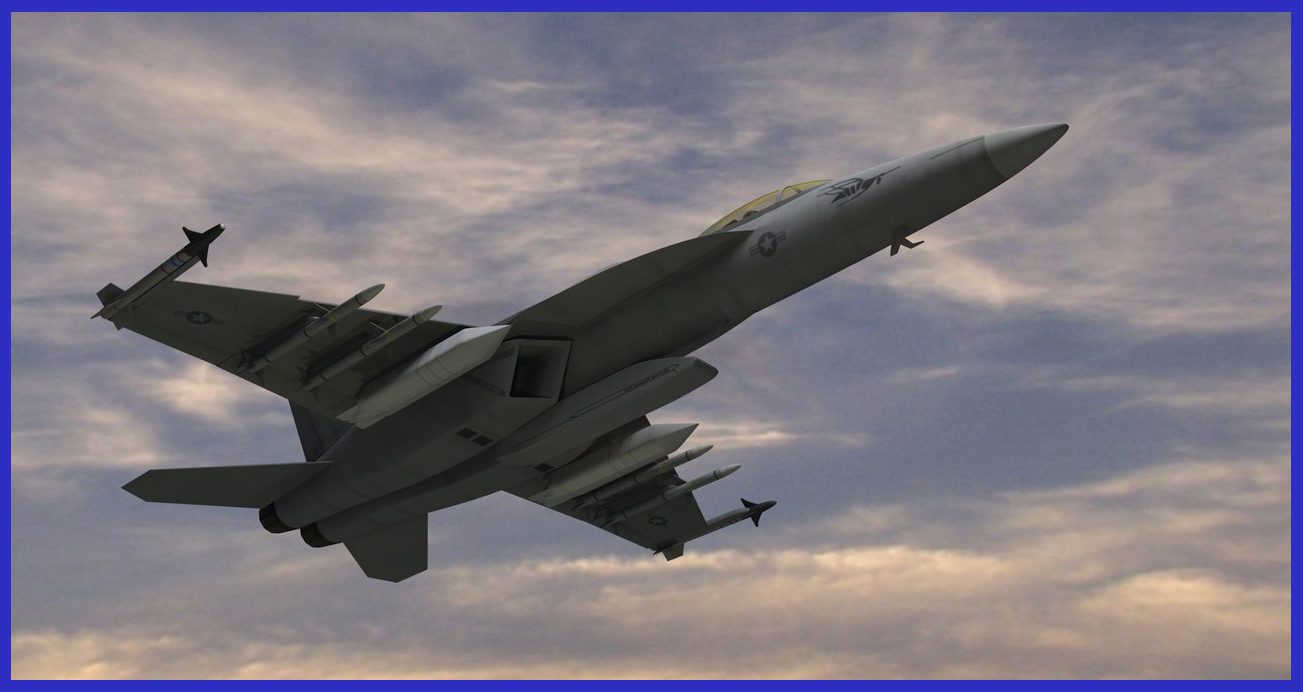
The Procurement Phase
Despite extensive testing and evaluations, the U.S. Government Accountability Office (GAO) expressed concerns in 2006, stating that they felt the electronic warfare systems on the EA-18G were not fully mature and required more time for development. The report also recommended that the Department of Defense (DoD) consider purchasing additional upgraded EA-6B Prowlers, allowing sufficient time for the EA-18G Growler to become fully functional.
Additionally, the GAO raised concerns about the crew onboard, as the original Prowler was operated by four crew members (one pilot and three electronic countermeasures officers), whereas the latest Growler is operated by just two crew members (a pilot and an Electronic Warfare Officer). However, this issue was addressed by Northrop Grumman’s advanced electronic countermeasure software systems, which do not require additional crew to operate.
The US Department of Defense (DoD) granted approval for the commencement of the EA-18G program’s low-rate initial production in 2007. Based on the commitments made, the EA-18G was originally slated to conclude its flight testing in 2008. During the initial stage, the Navy outlined its plan to procure approximately 85 aircraft in 2008. Anticipation for the approval of full-rate production was set for the third quarter of 2009, and it was ultimately granted on 23 November 2009.

After successful developmental testing, the EA-18G underwent operational testing, during which it was evaluated in real-world scenarios and operational environments. For instance, the aircraft was first used in combat during Operation Odyssey Dawn, where it played a crucial role in enforcing the UN no-fly zone over Libya in 2011. These tests effectively validated the aircraft’s mission effectiveness and performance in various combat scenarios.
In May 2010, Boeing and the US Department of Defense reached a mutually agreed-upon multi-year contract that encompassed an additional 66 F/A-18E/Fs and 58 EA-18Gs over the subsequent four years. As a result of this agreement, the total number of EA-18Gs on order is expected to cross 114. Moreover, in December 2014, the Navy publicly disclosed its intention to procure an additional 15 Growlers, signifying further expansion of the procurement plan.
Today, the EA-18G Growler continues to undergo updates and improvements to maintain its edge in electronic warfare capabilities, ensuring the protection and support of friendly forces while operating in highly contested and sophisticated electronic warfare environments.
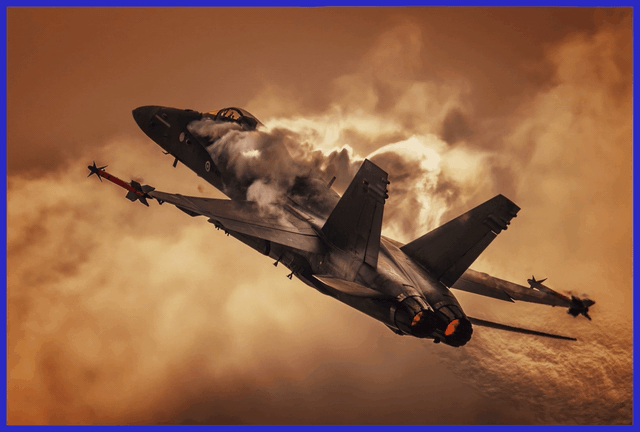
An Analysis of the Present-Day Boeing EA-18G Growler Design
The Growler’s main mission is to suppress and destroy enemy air defences and jam enemy radar and communications systems, thus providing a safer and more permissive environment for friendly forces to continue further strikes deep inside the enemy territory.
Design and Features:
Electronic Warfare Capabilities: The EA-18G Growler is a specialized aircraft designed for electronic warfare (EW) operations. Its flight performance closely resembles the F/A-18E/F, sharing over 95% of its aerodynamic design with the standard Super Hornet. This commonality allows for aggressive manoeuvrability in challenging situations, a capability the EA-6B Prowler lacked. Equipped with state-of-the-art electronic warfare systems, including jamming pods, radar warning receivers, and electronic countermeasures, it effectively suppresses enemy air defences and disrupts communication systems.
Carrier-Based Aircraft: The Growler is designed to operate from aircraft carriers, providing the capability to support naval operations and protect carrier strike groups. Its ability to take off and land on carriers makes it highly versatile for maritime operations. Additionally, the Royal Australian Air Force has been operating this aircraft since 2015.
Integrated Avionics: The aircraft features advanced avionics and mission systems for effective coordination with friendly aircraft and naval assets during missions. Most of the dedicated airborne electronic attack equipment is positioned on a plate in the area that formerly housed the internal 20 mm cannon and on the wingtips. Additionally, nine weapons stations allow for extra weapons or jamming pods. The aircraft’s electronic upgrades include AN/ALQ-218 wideband receivers on the wingtips, ALQ-99 high and low-band tactical jamming pods, and the Raytheon AN/APG-79 AESA radar. The integration of these pods forms a comprehensive electronic warfare suite, capable of detecting and jamming all known surface-to-air threats.
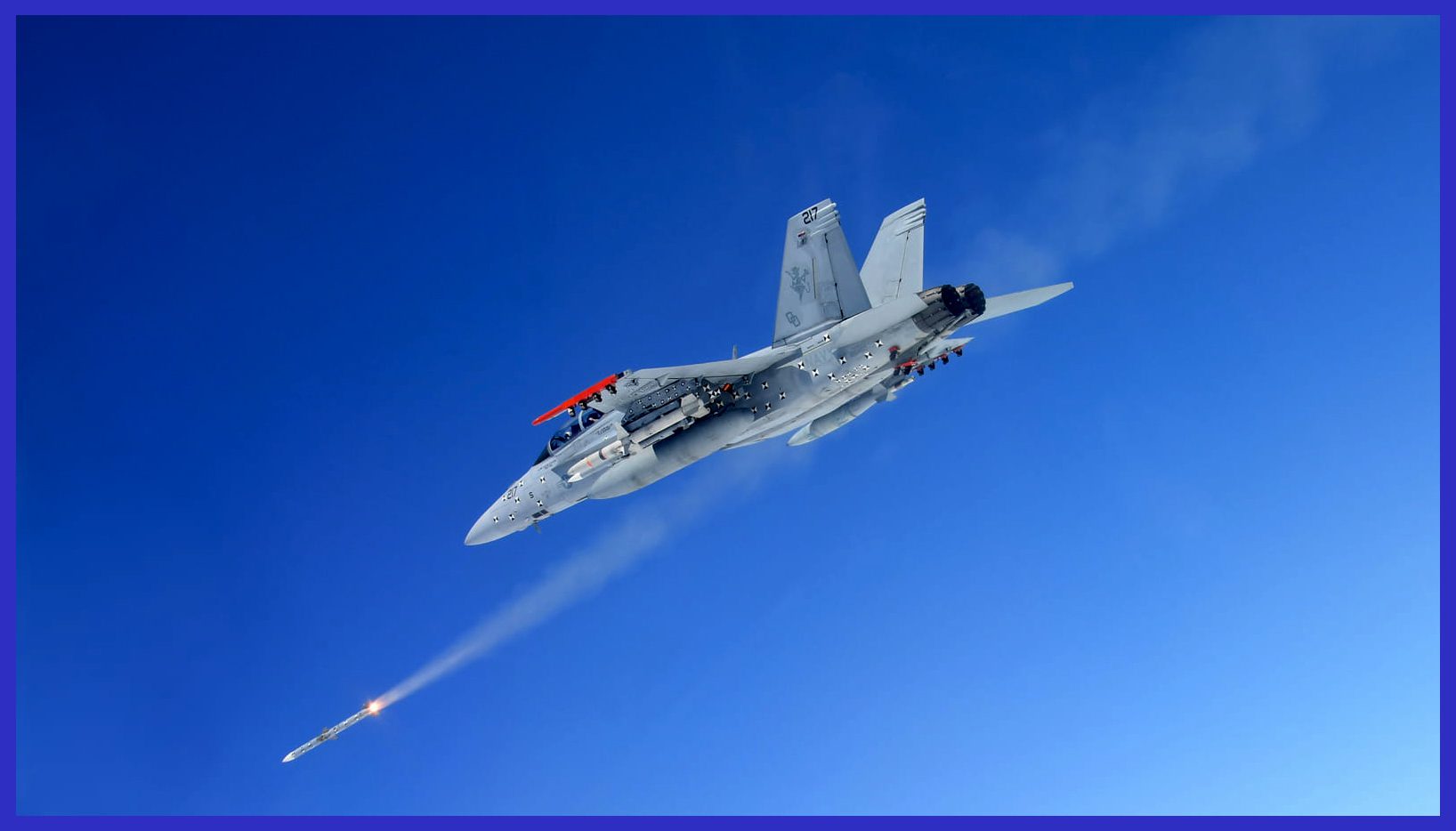
Armament: The EA-18G can carry a variety of air-to-air and air-to-ground weapons in addition to its electronic warfare systems, such as two AIM-120 AMRAAM and two AGM-88 HARM missiles. This capability enables it to engage enemy threats or provide support to friendly forces as needed.
Datalink Sensors: The EA-18G utilizes the INCANS ( Integrated Communications, Navigation, and Identification Avionics Suite ) Interference Cancellation system, allowing voice communication while jamming enemy communications, a capability that the EA-6B Prowler lacked. Alongside the radar warning and jamming equipment, the Growler is equipped with a communications receiver and jamming system, providing suppression and electronic attack against airborne communication threats. Notably, the Growler is the initial platform for the Next Generation Jammer (NGJ) program, incorporating Active Electronically Scanned Array (AESA) technology to precisely focus jamming power where needed. In December 2015, Boeing announced their plan to upgrade Navy EA-18Gs with the TTNT datalink.
Continuous Improvements: Over the years, the EA-18G Growler has undergone various upgrades and modernizations to enhance its capabilities and stay relevant in modern warfare scenarios as of 2023 and beyond for at least a decade.
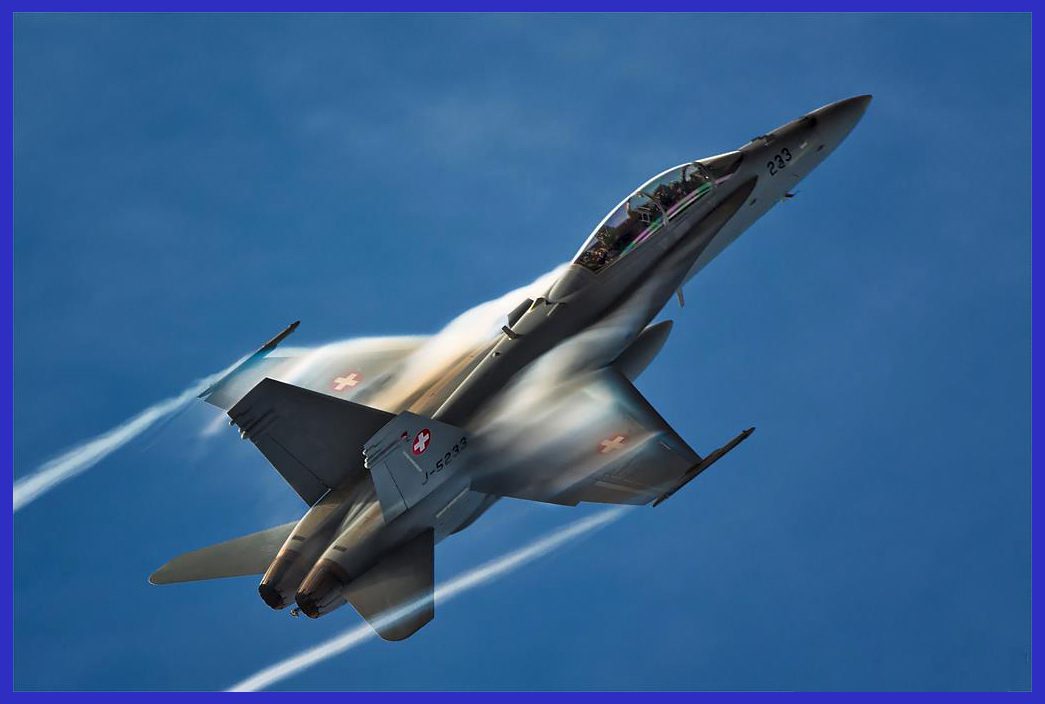
The Latest Generation Boeing F/A-18E/F Super Hornet and EA-18G Growler: Technical Specifications
- Country Of Origin: USA
- Crew: F/A-18E: 1 pilot, F/A-18F: 2 (pilot and weapon systems officer) / Growler: 2 (pilot and electronic warfare officer)
- Length: 60 ft 2 in ( 18.31 m )
- Wingspan: 44 ft 9 in ( 13.7 m )
- Height: 16 ft ( 4.9 m )
- Wing area: 500 sq ft ( 46.5 m2 )
- Empty Weight: F/A-18E: 14,552 kg ( 32,081 lb ) / Growler: 15,011 kg ( 33,094 lb )
- Max Takeoff Weight: 29,964 kg ( 66,000 lb )
- Max Weapons Payload: 8,050 kg ( 17,750 lb )
- Powerplant: 2 × General Electric F414-GE-400 turbofans, 14,000 lbf (62 kN) thrust each dry, 22,000 lbf (98 kN) with afterburner
- Max Speed: Mach 1.8 / 1,900 km/h ( 1,190 mph ) at 40,000 ft
- Combat range: The combat radius for interdiction missions ranges between 700 km to 900 km (435 mi to 560 mi) with 2 or 3, 480-gallon drop tanks
- Ferry range with external fuel: 3,330 km ( 2,069 mi ) without any ordinance
- Service ceiling: 50,000 ft ( 15,000 m )
- g limits: 7.5 g
- Service life: 8,000 to 10,000 hours, specifically meeting the Block-III standards.
- Armament: F/A-18E/F Super Hornet: Equipped with 1× 20 mm M61A2 Vulcan cannon boasting 412 rounds, and fortified with 11 hard points (including 2× wingtips, 6× under-wing, and 3× under-fuselage), the aircraft has an impressive Max payload capacity in combat of 17,750 lb (8,050 kg). Additionally, it boasts Carrier bring-back payload capabilities, even if the weapon remains unused: F/A-18E: 9,900 lb (4,491 kg), F/A-18F: 9,000 lb (4,082 kg). This remarkable fighter aircraft also offers the flexibility to carry various combinations of potent weapons, such as Sidewinder, AMRAAM, ASRAAM air-to-air missiles, Maverick, SLAM-ER, HARM, JASSM, JSOW air-to-surface missiles, Harpoon, LRASM anti-ship missiles, JDAM, Paveway, Rockeye II, and B61 Bombs.
- Armament: EA-18G Growler: As an electronic warfare aircraft, it has not been designed with guns. Nevertheless, it boasts a total of 9 hardpoints, comprising 6 under-wing and 3 under-fuselage stations, enabling a remarkable capacity of 17,750 lb (8,050 kg) for external fuel and ordnance. The aircraft’s two wingtips are equipped with dedicated AN/ALQ-218 detection pods, while the under-wing main mid-board pylons carry AN/ALQ-99 High Band Jamming Pods, one on each side. Additionally, 480-gallon drop tanks are positioned next to these pylons, and the outboard pylon is reserved for AGM-88 HARM missiles. Furthermore, the aircraft is equipped with two multi-mode conformal fuselage stations, intended for AIM-120 AMRAAM missiles, and it also features 1 centerline fuselage removable hardpoint for the AN/ALQ-99 Low Band Jamming Pod. Nevertheless, it’s important to note that these configurations might be subject to change depending on future requirements.
Furthermore, seize this exclusive opportunity to acquire the exquisite large-scale 1/72 premium die-cast models of the formidable McDonnell Douglas F/A-18 Hornet “Magpie Scheme” and the Boeing F/A-18E/F Super Hornet. These remarkable and iconic naval military jets, boasting an impeccable track record, are now available for purchase on AirModels with worldwide delivery. Click here now to secure your piece before the limited stock is depleted.
In conclusion, the F-18 Super Hornet and E/A-18 Growler have proven themselves as indispensable pillars of modern military aviation. Their exceptional performance, adaptability, and collaborative prowess exemplify the cutting-edge technology and strategic advantage that Boeing brings to the United States Navy and allied forces, further solidifying their position as cornerstones of air power for years to come.
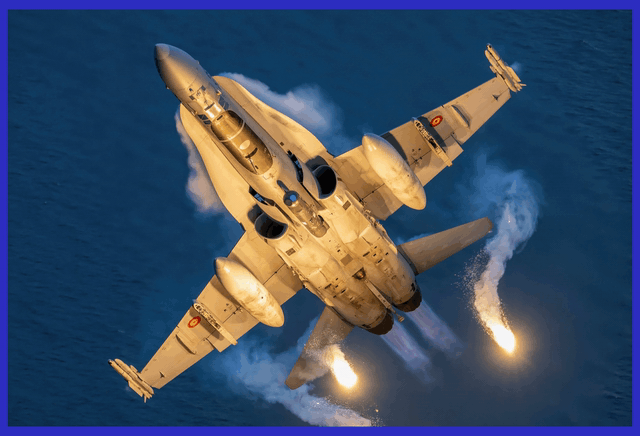
Important Announcement for Our Valued Readers!
After an article is published, it is possible that updates or changes may have occurred beyond the time of publication. Therefore, it is important to be aware that certain information in the article might be outdated. To ensure the most accurate analysis, it is highly recommended to verify the content with the latest sources available.
However, we are dedicated to delivering outstanding articles on military products and global updates. Maintaining quality and smooth operation requires resources. Your support sustains our efforts in providing insightful content. By purchasing high-quality products through our affiliated links, you help us keep our platform alive and acquire top-notch items. Your unwavering support is invaluable and inspires us to strive further.
We welcome your suggestions and requests for more information, as we value feedback from our readers. If there’s specific defence material or equipment not covered on our site, please share your request in the comments. We’ll strive to research and provide the required information. We sincerely thank you for your unwavering interest in our website, and we eagerly anticipate hearing from you! Enjoy your reading experience!